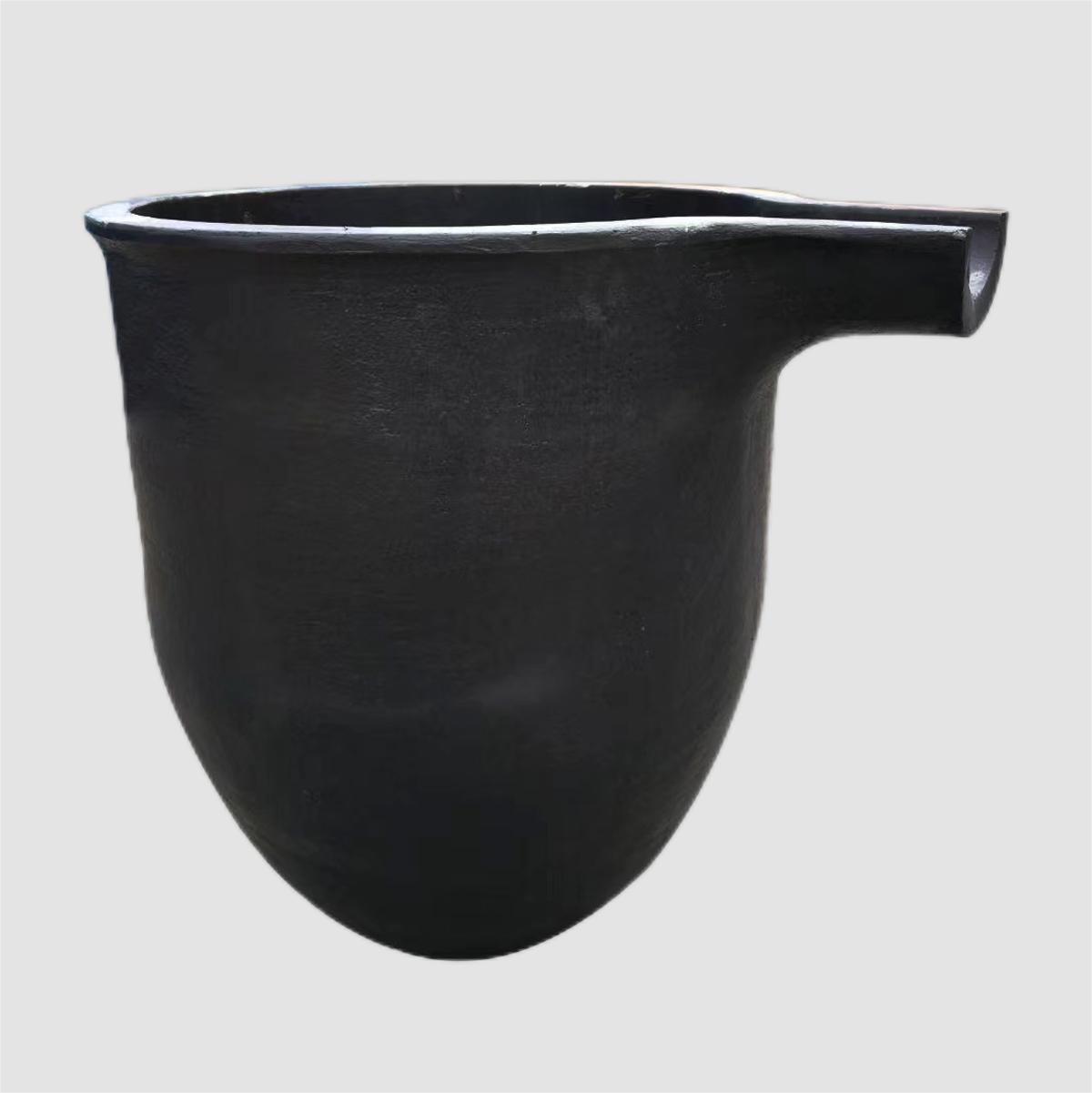
Isostatic Pressing Graphitist eine neue Art von Graphitmaterial, die in den 1960er Jahren entwickelt wurde und eine Reihe von hervorragenden Eigenschaften hat. Zum Beispiel hat isostatischer Pressegrafit einen guten Wärmewiderstand. In einer inerten Atmosphäre nimmt seine mechanische Festigkeit nicht nur mit zunehmender Temperatur zunimmt, sondern erhöht sich auch und erreicht seinen höchsten Wert bei etwa 2500 ° C. Im Vergleich zu gewöhnlichen Graphit ist seine Struktur fein und dicht und seine Gleichmäßigkeit gut; Der Wärmeleitungskoeffizient ist sehr niedrig und hat eine hervorragende thermische Schockfestigkeit. Isotrop; Starke chemische Korrosionsbeständigkeit, gute thermische und elektrische Leitfähigkeit; Hat eine ausgezeichnete mechanische Verarbeitungsleistung.
Genau aufgrund seiner hervorragenden Leistung wird in Bereichen wie Metallurgie, Chemie, Elektrik, Luft- und Raumfahrt und Atomergieindustrie weit verbreitet. Darüber hinaus wachsen die Anwendungsfelder mit der Entwicklung von Wissenschaft und Technologie ständig.
Produktionsprozess des isostatischen Pressegrafiten
Der Produktionsprozess von isostatischem Pressegraphit ist in Abbildung 1 dargestellt. Es ist offensichtlich, dass sich der Produktionsprozess des isostatischen Pressegraphits von der von Graphitelektroden unterscheidet.
Isostatic Pressing Graphit erfordert strukturell isotrope Rohstoffe, die in feinere Pulver gemahlen werden müssen. Kaltisostatische Pressungstechnologie muss angewendet werden, und der Bratzyklus ist sehr lang. Um die Zieldichte zu erreichen, sind multiple Imprägnierungsbratenzyklen erforderlich, und der Graphitisierungszyklus ist viel länger als der von gewöhnlichem Graphit.
Eine andere Methode zur Herstellung von isostatischem Pressgrafik ist die Verwendung von Mesophase -Kohlenstoffmikrokugeln als Rohstoffe. Erstens werden die Mesophase -Kohlenstoffmikrokugeln bei höheren Temperaturen einer Oxidationsstabilisierungsbehandlung unterzogen, gefolgt von einer isostatischen Presse, gefolgt von weiteren Kalzinierung und Graphitisierung. Diese Methode wird in diesem Artikel nicht eingeführt.
1.1 Rohstoffe
ThE -Rohstoffe zur Herstellung von isostatischen Pressgrafiken umfassen Aggregate und Bindemittel. Aggregate werden normalerweise aus Erdölkoks und Asphalt Cola sowie gemahlener Asphalt -Koks hergestellt. Zum Beispiel wird die von PoCO in den USA isostatische Graphit -Isostat -Graphit aus dem Boden Asphalt Coke Gilsontecoke hergestellt.
Um die Produktleistung nach verschiedenen Verwendungen anzupassen, werden auch Carbonschwarz und künstliche Graphit als Zusatzstoffe verwendet. Im Allgemeinen müssen Petroleum Coke und Asphalt Coke bei 1200 ~ 1400 ℃ kalkiniert werden, um vor dem Gebrauch Feuchtigkeit und flüchtige Materie zu entfernen.
Um die mechanischen Eigenschaften und die strukturelle Dichte von Produkten zu verbessern, gibt es jedoch auch eine direkte Produktion von isostatischen Pressegraphiten unter Verwendung von Rohstoffen wie Cola. Das Merkmal des Coking ist, dass es flüchtige Materie enthält, selbstgesintere Eigenschaften aufweist und synchron mit der Binder -Koks erweitert und zusammenbringt. Der Bindemittel verwendet in der Regel Kohle -Teer -Tonhöhe, und gemäß den verschiedenen Ausrüstungsbedingungen und den Prozessanforderungen jedes Unternehmens liegt der weicher Punkt der verwendeten Kohle -Teer -Tonhöhe von 50 ℃ bis 250 ° C.
Die Leistung von isostatischen Pressgrafiten wird stark von den Rohstoffen beeinflusst, und die Auswahl der Rohstoffe ist ein wichtiger Glied bei der Herstellung des erforderlichen Endprodukts. Vor der Fütterung müssen die Eigenschaften und Gleichmäßigkeit der Rohstoffe streng überprüft werden.
1.2 Schleifen
Die Gesamtgröße des isostatischen Pressegraphits ist normalerweise erforderlich, um unter 20um zu erreichen. Derzeit hat der raffinierteste isostatische Pressegraphit einen maximalen Partikeldurchmesser von 1 & mgr; m. Es ist sehr dünn.
Um aggregiertes Cola in ein solches feines Pulver zu mahlen, ist ein ultra-feiner Brecher erforderlich. Das Schleifen mit einer durchschnittlichen Partikelgröße von 10 bis 20 μ Das Pulver von m erfordert die Verwendung einer vertikalen Rollenmühle, wobei eine durchschnittliche Partikelgröße von weniger als 10 & mgr; das Pulver von m die Verwendung eines Luftströmungsschleifers erfordert.
1.3 Mischen und Kneten
Setzen Sie den Bodenpulver und den Kohle -Teer -Pech -Bindemittel proportional in einen Heizmischer zum Kneten ein, so dass eine Asphaltschicht gleichmäßig an der Oberfläche der Pulver -Koks -Partikel haftet. Entfernen Sie nach dem Kneten die Paste und lassen Sie sie abkühlen.
Postzeit: Sep-27-2023