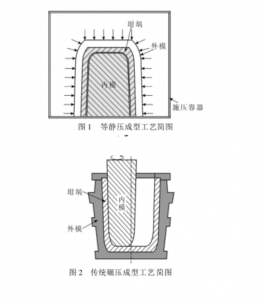
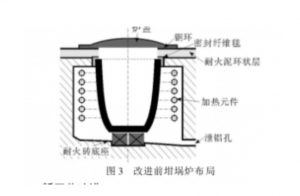
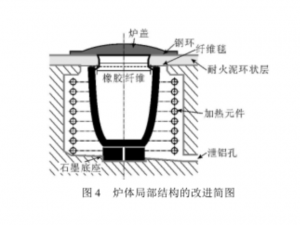
Die Produktion von Graphit Crucible hat sich mit dem Aufkommen der isostatischen Pressetechnologie erheblich entwickelt und sie als die weltweit fortschrittlichste Technik markiert. Im Vergleich zu herkömmlichen Ramming -Methoden führt isostatische Presse zu Tiegel mit gleichmäßiger Textur, höherer Dichte, Energieeffizienz und überlegener Oxidationsresistenz. Die Anwendung des hohen Drucks während des Formens verbessert die Textur des Tiegels erheblich, verringert die Porosität und steigert anschließend die thermische Leitfähigkeit und Korrosionsbeständigkeit, wie in Abbildung 1 dargestellt. In einer isostatischen Umgebung erfährt jeder Teil des Tiegels einen gleichmäßigen Formdruck, der überwidrig ist. Diese in Abbildung 2 dargestellte Methode übertrifft den traditionellen Rammingprozess, was zu einer erheblichen Verbesserung der Tiegelleistung führt.
1. Problemanweisung
Ein Problem tritt im Kontext eines Aluminiumlegierungs -Isolationswiderstands -Tiegelofens unter Verwendung von Rammed Graphit Tiegel mit einer Lebensdauer von ca. 45 Tagen auf. Nach nur 20 Tagen der Verwendung wird ein spürbarer Rückgang der thermischen Leitfähigkeit beobachtet, begleitet von Mikro-Cracks auf der Außenoberfläche des Schmelzbare. In den späteren Nutzungsstadien ist ein schwerer Rückgang der thermischen Leitfähigkeit offensichtlich, was den Schmelztiegel nahezu nicht leitend macht. Zusätzlich entwickeln sich mehrere Oberflächenrisse, und aufgrund der Oxidation tritt an der Oberseite des Tiegels auf.
Bei der Prüfung des Tiegelofens, wie in Abbildung 3 gezeigt, wird eine Basis aus gestapelten feuerfesten Ziegeln verwendet, wobei das Bottommost -Erwärmungselement des Widerstandsdrahtes 100 mm über der Basis liegt. Die Oberseite des Tiegels wird mit Asbestfaserdecken versiegelt, die etwa 50 mm von der Außenkante entfernt positioniert sind, wodurch ein signifikanter Abrieb am inneren Rand des Tiegel -Oberteils aufweist.
2. Neue technologische Verbesserungen
Verbesserung 1: Übernahme von isostatisch gepresstem Tongrafit Tiegel (mit oxidationsresistenter Glasur mit niedriger Temperatur))
Die Nutzung dieses Schmelztiegels verbessert seine Anwendung in Aluminiumlegierungsdämmöfen, insbesondere in Bezug auf die Oxidationsresistenz, erheblich. Graphitkreuzer oxidieren typischerweise bei Temperaturen über 400 ° C, während die Isolierungstemperatur von Aluminiumlegieröfen zwischen 650 und 700 ℃ liegt. Tiegel mit niedriger Temperatur oxidationsresistenter Glasur können den Oxidationsprozess bei Temperaturen über 600 ° C wirksam verlangsamen, um eine längere hervorragende thermische Leitfähigkeit zu gewährleisten. Gleichzeitig verhindert es die Festigkeitsreduktion aufgrund von Oxidation und verlängert die Lebensdauer des Schmelzbars.
Verbesserung 2: Ofenbasis unter Verwendung von Graphit des gleichen Materials wie der Schmelztiegel
Wie in Abbildung 4 dargestellt, sorgt unter Verwendung einer Graphitbasis des gleichen Materials wie der Schmelztiegel eine gleichmäßige Erwärmung des Tiegel -Bodens während des Heizprozesses. Dies mildert Temperaturgradienten, die durch ungleichmäßiges Erhitzen verursacht werden, und verringert die Tendenz zu Rissen, die durch ungleichmäßiges Bodenheizung resultieren. Die dedizierte Graphitbasis garantiert auch eine stabile Unterstützung für den Schmelztiegel, der sich mit ihrem Boden ausrichtet und stressinduzierte Frakturen minimiert.
Verbesserung 3: Lokale strukturelle Verbesserungen des Ofens (Abbildung 4)
- Verbesserte innere Kante der Ofenabdeckung, wodurch der Verschleiß am Tiegel der Oberstiche effektiv verhindert wird und die Ofenversiegelung erheblich verbessert.
- Die Gewährleistung des Widerstandsdrahtes ist mit dem Grund des Schmelztiegels auf Platz und garantiert eine ausreichende Bodenheizung.
- Minimierung der Auswirkung von Top-Faserdeckendichtungen auf das Tiegelheizung, sorgen für eine angemessene Erwärmung an der Oberseite des Tiegels und die Verringerung der Auswirkungen der Niedrigtemperaturoxidation.
Verbesserung 4: Verfeinerung des Schmelzverbrauchsprozesses
Vor der Nutzung den Schmelztiegel im Ofen bei Temperaturen unter 200 ° C für 1-2 Stunden vorheizen, um die Feuchtigkeit zu beseitigen. Steigern Sie nach dem Vorheizen die Temperatur schnell auf 850-900 ℃ und minimieren Sie die Verweilzeit zwischen 300 und 600 ° C, um die Oxidation innerhalb dieses Temperaturbereichs zu verringern. Senken Sie anschließend die Temperatur auf die Arbeitstemperatur und führen Sie Aluminiumflüssigkeitsmaterial für den normalen Betrieb ein.
Folgen Sie aufgrund der korrosiven Auswirkungen von Raffineriermitteln auf Tiegel der korrekten Verwendungsprotokolle. Die regelmäßige Schlackenentfernung ist unerlässlich und sollte durchgeführt werden, wenn der Schmelztiegel heiß ist, da die Reinigungsschlacke ansonsten schwierig wird. Wachsame Beobachtung der thermischen Leitfähigkeit des Schmelzbars und das Vorhandensein des Alterns an den Schmelzwänden ist in den späteren Nutzungsstadien von entscheidender Bedeutung. Es sollten rechtzeitig ersetzt werden, um unnötige Energieverluste und Aluminiumflüssigkeitsleckage zu vermeiden.
3.. Verbesserungsergebnisse
Die verlängerte Lebensdauer des verbesserten Tiegels ist bemerkenswert, wodurch die thermische Leitfähigkeit für längere Dauer aufrechterhalten wird, ohne dass die Oberflächenrisse beobachtet werden. Das Feedback der Benutzer zeigt eine verbesserte Leistung an und senkt nicht nur die Produktionskosten, sondern auch die Produktionseffizienz erheblich.
4. Schlussfolgerung
- Isostatisch gepresste Tongrafitiskreuze übertreffen traditionelle Tiegel in Bezug auf die Leistung.
- Die Ofenstruktur sollte der Größe und Struktur des Schmelzkreises für eine optimale Leistung übereinstimmen.
- Die ordnungsgemäße Nutzung des Tiegels verlängert die Lebensdauer erheblich und kontrolliert die Produktionskosten effektiv.
Durch sorgfältige Forschung und Optimierung der Schmelzofen -Technologie tragen die verbesserte Leistung und die Lebensdauer intensiv zu erhöhten Produktionseffizienz und Kosteneinsparungen bei.
Postzeit: Dez.-24-2023