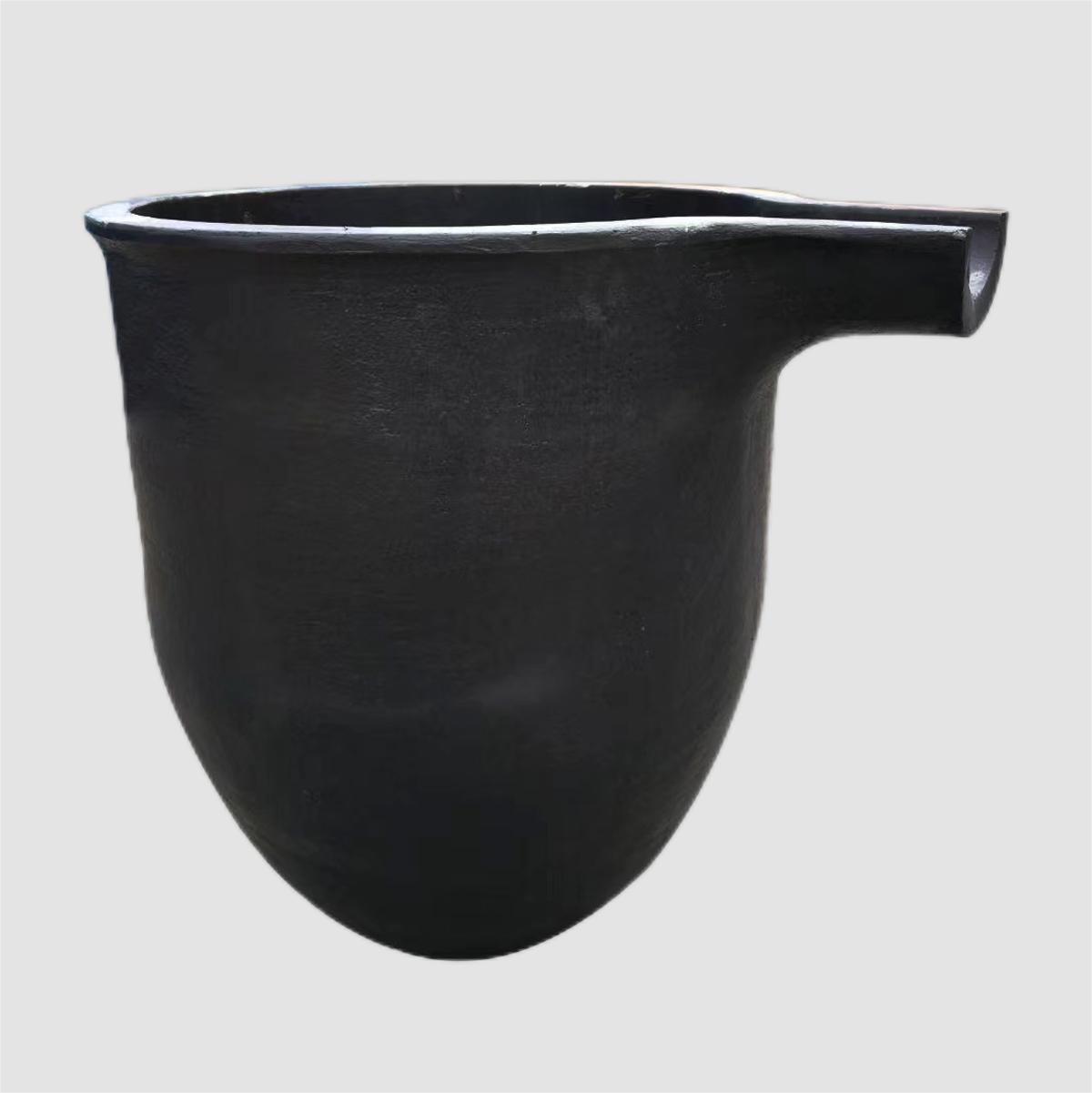
1.4 Sekundärschleifen
Die Paste wird zerkleinert, gemahlen und in Partikel mit einer Größe von mehreren zehn bis hundert Mikrometern gesiebt, bevor sie gleichmäßig vermischt wird.Es wird als Pressmaterial, Presspulver genannt, verwendet.Die Ausrüstung für die Sekundärmahlung verwendet normalerweise eine vertikale Walzenmühle oder eine Kugelmühle.
1.5 Umformung
Im Gegensatz zu gewöhnlichem Extrudieren und Formenisostatisch gepresster Graphitwird mittels kaltisostatischer Presstechnik geformt (Abbildung 2).Füllen Sie das Rohmaterialpulver in die Gummiform und verdichten Sie das Pulver durch hochfrequente elektromagnetische Vibration.Saugen Sie die Pulverpartikel nach dem Versiegeln ab, um die Luft zwischen ihnen herauszulassen.Legen Sie es in einen Hochdruckbehälter mit flüssigen Medien wie Wasser oder Öl, setzen Sie es auf 100–200 MPa unter Druck und pressen Sie es zu einem zylindrischen oder rechteckigen Produkt.
Nach dem Prinzip von Pascal wird durch ein flüssiges Medium wie Wasser Druck auf eine Gummiform ausgeübt, und der Druck ist in alle Richtungen gleich.Dadurch werden die Pulverpartikel in der Form nicht in Füllrichtung ausgerichtet, sondern in unregelmäßiger Anordnung verdichtet.Obwohl Graphit in seinen kristallographischen Eigenschaften anisotrop ist, ist der isostatisch gepresste Graphit insgesamt isotrop.Die geformten Produkte haben nicht nur zylindrische und rechteckige Formen, sondern auch zylindrische und Tiegelformen.
Die isostatische Pressformmaschine wird hauptsächlich in der Pulvermetallurgieindustrie eingesetzt.Aufgrund der Nachfrage von High-End-Industrien wie Luft- und Raumfahrt, Nuklearindustrie, Hartlegierungen und Hochspannungselektromagnetik schreitet die Entwicklung der isostatischen Presstechnologie sehr schnell voran und es besteht die Möglichkeit, kaltisostatische Pressmaschinen mit einem Arbeitszylinder herzustellen Innendurchmesser von 3000 mm, eine Höhe von 5000 mm und ein maximaler Arbeitsdruck von 600 MPa.Derzeit betragen die maximalen Spezifikationen für kaltisostatische Pressmaschinen, die in der Kohlenstoffindustrie zur Herstellung von isostatisch gepresstem Graphit eingesetzt werden, Φ 2150 mm × 4700 mm bei einem maximalen Arbeitsdruck von 180 MPa.
1.6 Backen
Während des Röstvorgangs kommt es zu einer komplexen chemischen Reaktion zwischen dem Zuschlagstoff und dem Bindemittel, die dazu führt, dass sich das Bindemittel zersetzt und eine große Menge flüchtiger Stoffe freisetzt, während gleichzeitig eine Kondensationsreaktion stattfindet.In der Niedertemperatur-Vorwärmstufe dehnt sich das Rohprodukt durch die Erhitzung aus und im anschließenden Erhitzungsprozess schrumpft das Volumen aufgrund der Kondensationsreaktion.
Je größer das Volumen des Rohprodukts ist, desto schwieriger ist es, flüchtige Stoffe freizusetzen, und die Oberfläche und das Innere des Rohprodukts sind anfällig für Temperaturunterschiede, ungleichmäßige Wärmeausdehnung und -kontraktion, was zu Rissen im Rohprodukt führen kann.
Aufgrund seiner feinen Struktur erfordert isostatisch gepresster Graphit einen besonders langsamen Röstprozess, und die Temperatur im Ofen sollte sehr gleichmäßig sein, insbesondere während der Temperaturphase, in der flüchtige Asphaltbestandteile schnell austreten.Der Aufheizvorgang sollte mit Vorsicht durchgeführt werden, mit einer Aufheizrate von nicht mehr als 1 ℃/h und einem Temperaturunterschied im Ofen von weniger als 20 ℃.Dieser Vorgang dauert etwa 1-2 Monate.
1.7 Imprägnierung
Beim Rösten werden die flüchtigen Bestandteile des Steinkohlenteerpechs freigesetzt.Bei der Gasentladung und Volumenkontraktion bleiben im Produkt feine Poren zurück, bei denen es sich nahezu ausschließlich um offene Poren handelt.
Um die Volumendichte, mechanische Festigkeit, Leitfähigkeit, Wärmeleitfähigkeit und chemische Beständigkeit des Produkts zu verbessern, kann das Druckimprägnierungsverfahren verwendet werden, bei dem Kohlenteerpech durch offene Poren in das Innere des Produkts imprägniert wird.
Das Produkt muss zunächst vorgewärmt und anschließend im Imprägniertank abgesaugt und entgast werden.Anschließend wird der geschmolzene Kohlenteerasphalt in den Imprägniertank gegeben und unter Druck gesetzt, damit der Imprägniermittelasphalt in das Innere des Produkts eindringen kann.Normalerweise durchläuft isostatisch gepresster Graphit mehrere Imprägnierungsröstzyklen.
1.8 Graphitisierung
Erhitzen Sie das kalzinierte Produkt auf etwa 3000 °C, ordnen Sie das Gitter der Kohlenstoffatome geordnet an und schließen Sie die Umwandlung von Kohlenstoff in Graphit ab, die als Graphitierung bezeichnet wird.
Zu den Graphitisierungsmethoden gehören die Acheson-Methode, die interne thermische Reihenverbindungsmethode, die Hochfrequenz-Induktionsmethode usw. Der übliche Acheson-Prozess dauert etwa 1–1,5 Monate, bis die Produkte in den Ofen geladen und aus ihm entnommen werden.Jeder Ofen kann mehrere Tonnen bis Dutzende Tonnen Röstprodukte verarbeiten.
Zeitpunkt der Veröffentlichung: 29.09.2023