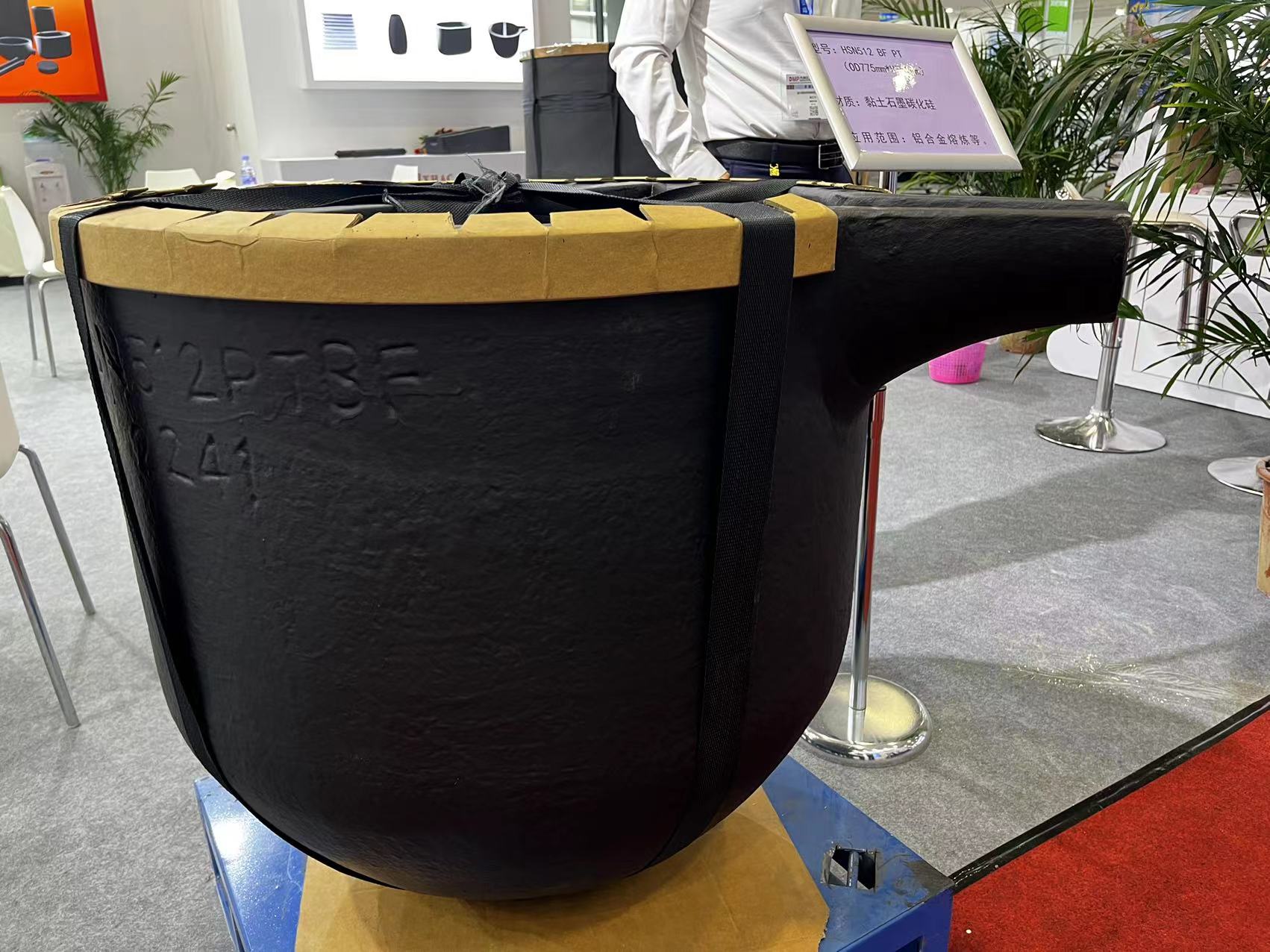
In der Welt der Metallurgie und der Materialwissenschaft,der Schmelztiegelist ein wesentliches Werkzeug zum Schmelzen und Gießen von Metallen. Unter den verschiedenen Arten von Tiegel sind Graphit Silicium Carbid (sic) Tiegel für ihre außergewöhnlichen Eigenschaften wie hohe thermische Leitfähigkeit, hervorragende thermische Schockresistenz und überlegene chemische Stabilität hervorzuheben. In diesem Artikel werden wir uns mit dem Rezept für Graphit-SIC-Tiegel eintauchen und untersuchen, wie ihre Komposition zu ihrer bemerkenswerten Leistung in Hochtemperaturanwendungen beiträgt.
Die grundlegenden Zutaten
Die primären Komponenten von Graphit -Sic -Tiegel sind Flockengrafit- und Siliziumkarbid. Flockengrafit, der normalerweise 40% -50% des Schmelztiegels ausmacht, bietet eine hervorragende thermische Leitfähigkeit und Schmierung, die bei der einfachen Freisetzung des Gussmetalls hilft. Siliziumkarbid, das 20% -50% des Schmelztiegels ausmacht, ist für die hohe thermische Schockbeständigkeit und die chemische Stabilität des Crucible bei erhöhten Temperaturen verantwortlich.
Zusätzliche Komponenten für eine verbesserte Leistung
Um die Hochtemperaturleistung und chemische Stabilität des Schmelztiegels weiter zu verbessern, werden dem Rezept zusätzliche Komponenten hinzugefügt:
- Elementares Siliziumpulver (4%-10%): Verbessert die Hochtemperaturfestigkeit und Oxidationsresistenz des Schmelzbars.
- Borkarbidpulver (1%-5%): Erhöht die chemische Stabilität und Resistenz gegen korrosive Metalle.
- Ton (5%-15%): fungiert als Bindemittel und verbessert die mechanische Festigkeit und thermische Stabilität des Schmelztiegels.
- Thermosettierungsbindemittel (5%-10%): Hilft bei der Bindung aller Komponenten zusammen, um eine zusammenhängende Struktur zu bilden.
Die High-End-Formel
Für Anwendungen, die eine noch höhere Leistung fordern, wird eine High-End-Graphit-Tiegelformel verwendet. Diese Formel umfasst 98% Graphitpartikel, 2% Calciumoxid, 1% Zirkoniumoxid, 1% Borsäure, 1% Natriumsilikat und 1% Aluminiumsilikat. Diese zusätzlichen Inhaltsstoffe bieten eine beispiellose Resistenz gegen hohe Temperaturen und aggressive chemische Umgebungen.
Herstellungsprozess
Die Vorbereitung von Graphit -Sic Tiegel beinhaltet einen akribischen Prozess. Anfänglich werden Flockengrafit- und Siliziumcarbid gründlich gemischt. Anschließend werden elementares Siliziumpulver, Borkarbidpulver, Ton und der Thermosettungsbindemittel zur Mischung gegeben. Die Mischung wird dann mit einer Kaltpressenmaschine in Form gedrückt. Schließlich werden die geformten Tiegel in einen Hochtemperaturofen gesintert, um ihre mechanische Festigkeit und thermische Stabilität zu verbessern.
Anwendungen und Vorteile
In der metallurgischen Industrie werden in der metallurgischen Branche häufig Metalle wie Eisen, Stahl, Kupfer und Aluminium ausgesetzt. Ihre überlegene thermische Leitfähigkeit sorgt für ein gleichmäßiges Erwärmen und verringert den Energieverbrauch. Der hohe thermische Schockwiderstand minimiert das Risiko eines Risses bei schnellen Temperaturveränderungen, während ihre chemische Stabilität die Reinheit des geschmolzenen Metalls sicherstellt.
Zusammenfassend ist das Rezept für Graphit-Silizium-Carbid-Tiegel eine fein abgestimmte Mischung aus Materialien, die ein Gleichgewicht zwischen thermischer Leitfähigkeit, thermischer Schockfestigkeit und chemischer Stabilität bieten. Diese Komposition macht sie im Bereich der Metallurgie unverzichtbar, wo sie eine entscheidende Rolle beim effizienten und zuverlässigen Schmelzen und Gießen von Metallen spielen.
Durch das Verständnis der Komponenten und des Herstellungsprozesses von Graphit -SIC -Tiegel können die Industrien fundierte Entscheidungen für ihre spezifischen Anwendungen treffen und eine optimale Leistung und Langlebigkeit ihrer Tiegel sicherstellen. Mit dem Fortschritt der Technologie werden weitere Verbesserungen der Rezept- und Herstellungstechniken von Graphit -Sic -Texten erwartet, was den Weg für noch effizientere und nachhaltigere metallurgische Prozesse ebnet.
Postzeit: März-2024